welding rear diff
welding rear diff
Does the metal need to be heated before welding because it is high tensile?
Where abouts is the best place to weld the spider gears so they dont spin?
Where abouts is the best place to weld the spider gears so they dont spin?
88 L series Sports Wagon, Weber 32/36 carby, 2" Lift Kit, King Springs all round, 14" Desert Rats, 27" Super Trippers, Welded Rear Diff, Dark tint, JVC Mp3 Deck.
i have heard that welding a bolt in the gears is the best bet.... don't ask me where though. *shrugs*
Dave
Dave
EJ conversion wiring harness cut downs available. Please PM or email ([email protected]) for details.
heating the spider gears firse helps to get a good deep weld cos its tricky to get in there
but get as deep into the spider gears as u can with the welder and try and get everything nicely glowing together
you can also weld some nuts and bolts and other bits of metal in there to fill some gaps so theres no chance of the spider gears moving
i welded a plate on both sides of the spider gears so it was all welded together like a solid box
easily smahed axles with no signs of damaging the diff
but get as deep into the spider gears as u can with the welder and try and get everything nicely glowing together
you can also weld some nuts and bolts and other bits of metal in there to fill some gaps so theres no chance of the spider gears moving
i welded a plate on both sides of the spider gears so it was all welded together like a solid box
easily smahed axles with no signs of damaging the diff

hmm,me starting to ponder about this........hey bluesteel, how big welder did you need?
i have a sip120, think that would do ?
otherwise is it possible to remove the diff (and drive shaft), and still drive ?
Then when you normally drive without one of the half shafts, do you protect the axle stubs ends with anything ? weather will cause rust?
i have a sip120, think that would do ?
otherwise is it possible to remove the diff (and drive shaft), and still drive ?
Then when you normally drive without one of the half shafts, do you protect the axle stubs ends with anything ? weather will cause rust?
, haha, i'm not that stupid, but I called it drive shaft! yeah with it removed too.Suba wrote:If you removed the rear diff you would have a problem as what to do with the tailshaft as there would be nothing to support it , as far as the stub axle you wouldnt really need to do anything to them allthough some crc wouldn't hurt and may make it easier to replace and remove when required.
Mike.
In theory should be ok, I just wonder if the gearbox will cope with no shaft attached?
- Suba
- General Member
- Posts: 1301
- Joined: Tue Oct 04, 2005 10:00 am
- Location: Seville Grove . Western Australia.
- Contact:
The box would cope fine , if however you left both rear axel shafts in with the diff spider gear welded ,you would do some nasty things to your gearbox due to the strain , it would however more than likely break one of the rear cv's before you broke the gearbox.
With the spider gear welded and one rear axel removed you will still have drive to one rear wheel when you select 4wd.
Mike.
With the spider gear welded and one rear axel removed you will still have drive to one rear wheel when you select 4wd.
Mike.


without proper preheat, around 350deg, the weld will crack. If I was going to weld one up without proper preheat, I would use 18-8 stainless steel electrodes as they will absorb a bit of shock without cracking. some 302 rods will do it well. Pour it in and hope it sticks.
If it can't be cut, welded or re-machined, you probably don't need it.
It would also help heaps if you remove the diff centre from the housing.
This is very easy to do (but does require a special socket to remove the stub axels). You'd have a much easier job of getting access to all the areas you need to weld.
This is very easy to do (but does require a special socket to remove the stub axels). You'd have a much easier job of getting access to all the areas you need to weld.
EZ30 L series - Monsterwagon
https://www.ausubaru.com.au/viewtopic.php?f=71&t=26163
https://www.ausubaru.com.au/viewtopic.php?f=71&t=26163
What ratio diff do you want welded ?
I have a 3.9 here I might wack with the stainless mig....the blobs of weld you get off this thing make lumps that are as hard as a 10 grade bolt, so it should hang in there !
....I`d be looking form ~$75 once its welded !
OS
I have a 3.9 here I might wack with the stainless mig....the blobs of weld you get off this thing make lumps that are as hard as a 10 grade bolt, so it should hang in there !
....I`d be looking form ~$75 once its welded !
OS
MY05 GT-STI DCCD 6spd 13.88at98.7
88 FJ62 Cruiser-5.0ChevTPI TT,6psi,Hi6,044,Wolf3dV4,FMIC
88 FJ62 Cruiser-5.0ChevTPI TT,6psi,Hi6,044,Wolf3dV4,FMIC
is this referring to rods for a arc welder ? thought they were only real good for mild steels........?cameron wrote:without proper preheat, around 350deg, the weld will crack. If I was going to weld one up without proper preheat, I would use 18-8 stainless steel electrodes as they will absorb a bit of shock without cracking. some 302 rods will do it well. Pour it in and hope it sticks.
- AlpineRaven
- Senior Member
- Posts: 3682
- Joined: Wed Oct 19, 2005 10:00 am
- Location: Melbourne, Victoria, Australia.
I have welded diff, used on my Liberty while on off road mission but hated it on cornering road and took it out put back open diff, been on the shelf for a while, all yours for $50 (but regretted myself for taking it out - wanna VLSD again now)
Cheers
AP
Cheers
AP
Subarus that I have/had:
1995 Liberty "Rallye" - 5MT AWD, LSD - *written off 25/8/06 in towing accident.
1996 Liberty Wagon - SkiFX AWD 5MT D/R, Lifted.. Outback Sway Bar, 1.59:1 Low Gearing see thread: 1.59:1 in EJ Box Page
Sold at 385,000kms in July 2011.
2007 Liberty BP Wagon, 2.5i automatic
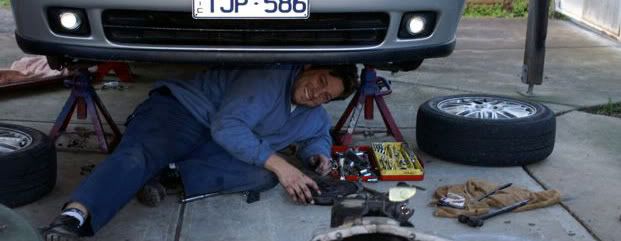
1995 Liberty "Rallye" - 5MT AWD, LSD - *written off 25/8/06 in towing accident.
1996 Liberty Wagon - SkiFX AWD 5MT D/R, Lifted.. Outback Sway Bar, 1.59:1 Low Gearing see thread: 1.59:1 in EJ Box Page
Sold at 385,000kms in July 2011.
2007 Liberty BP Wagon, 2.5i automatic
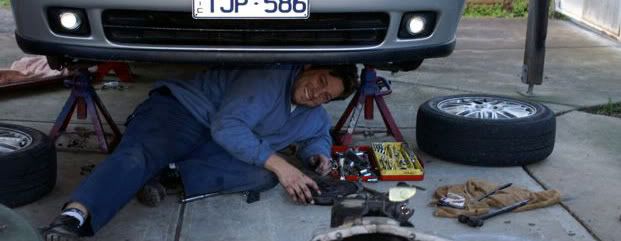