
I've had a multi process inverter machine for some years now but never anywhere proper like a metal work bench for laying out fabrication jobs, marking out, cutting, grinding, welding etc. I've always got by with a work mate with a plate of aluminium sat on top of it

The Stronghand tools Nomad welding table is the answer to all my problems. It is a lightweight, collapsible flat pack welding and fabrication table. The table surface is something like 3mm (thick enough, but don't go hammering on it) with slots in it for placing clamps. There are 2 fences or side rails that can come up and act as guide rails for clamping things up nice and square for tacking. The table is height adjustable and tilt adjustable which can come in handy sometimes, if you want to weld something that is in an awkward position normally but you don't want to un-clamp it from the table. The whole thing weighs something like 20 kgs or so and has wheels so when its folded up you can just grab the handle, tilt it over and wheel it around.
I got this recently as I need to make a trolley to put my welder and gas bottle on but have been putting it off for ages (years) because I have nowhere decent to fabricate it. Today I spent a full day working on the table framing up the sides of my trolley and it is absolutely brilliant. With a few wide reach vice grip type clamps it is almost magical how easily and quickly things go together. The slots mean you almost always have somewhere to put a clamp even in the middle of the table. The right angle fences came in handy many times for tacking things up nice and square. And when the job is all said and done for the day the table folds flat and stores neatly away

The whole top is zinc coated I think, or passivated as it has a very bright gold kind of finish. This scratches off easily and welding spatter WILL stick to it so it is important to keep the top protected with a quick spray of anti-spatter or WD-40.
5 hours work got both side frames for the trolley finished, alot of time was spent cutting pieces to length and doing the miter joints. All marked out with a square, scribe and cut with an angle grinder. What I wouldn't give for a band saw or drop saw!
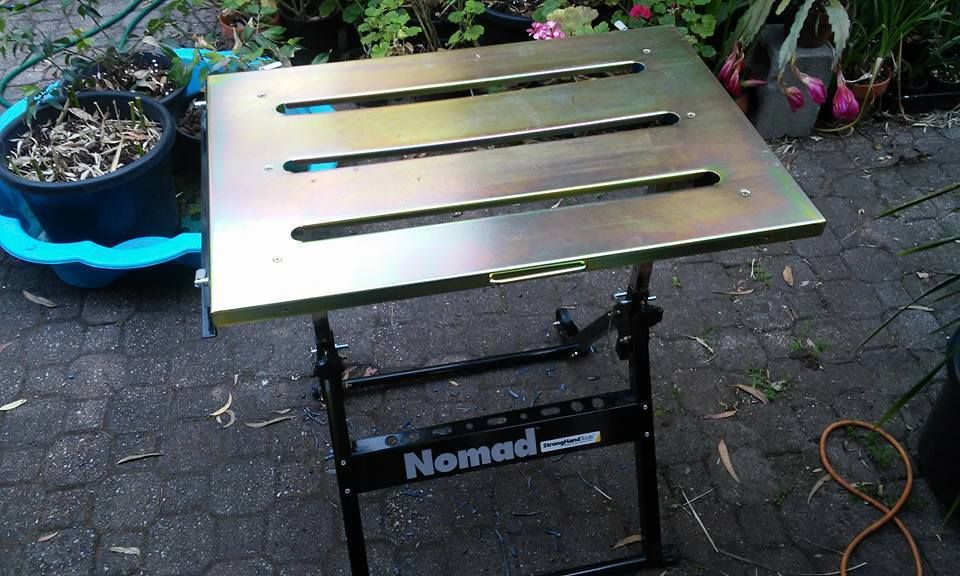
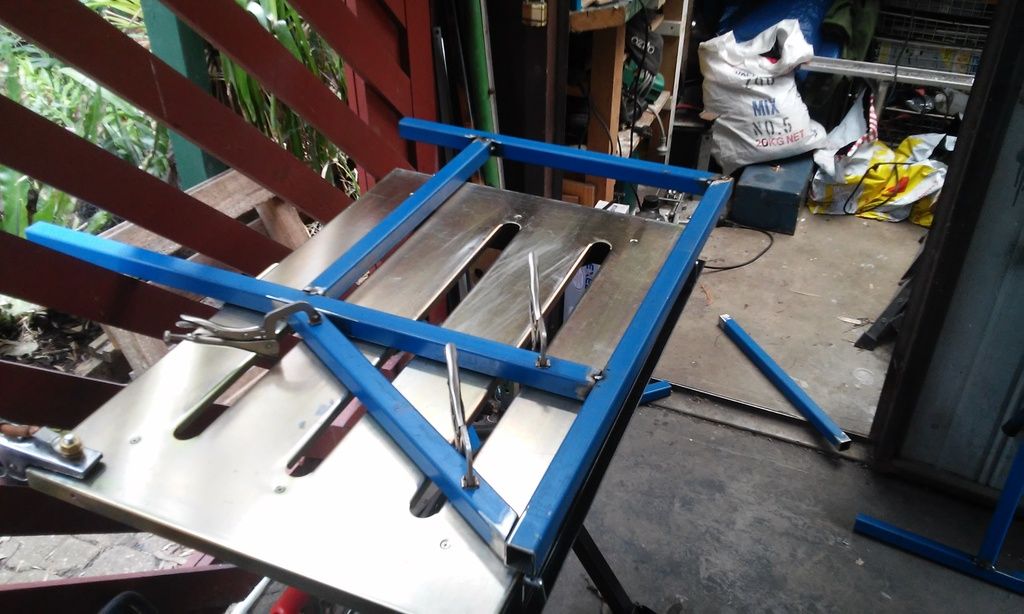
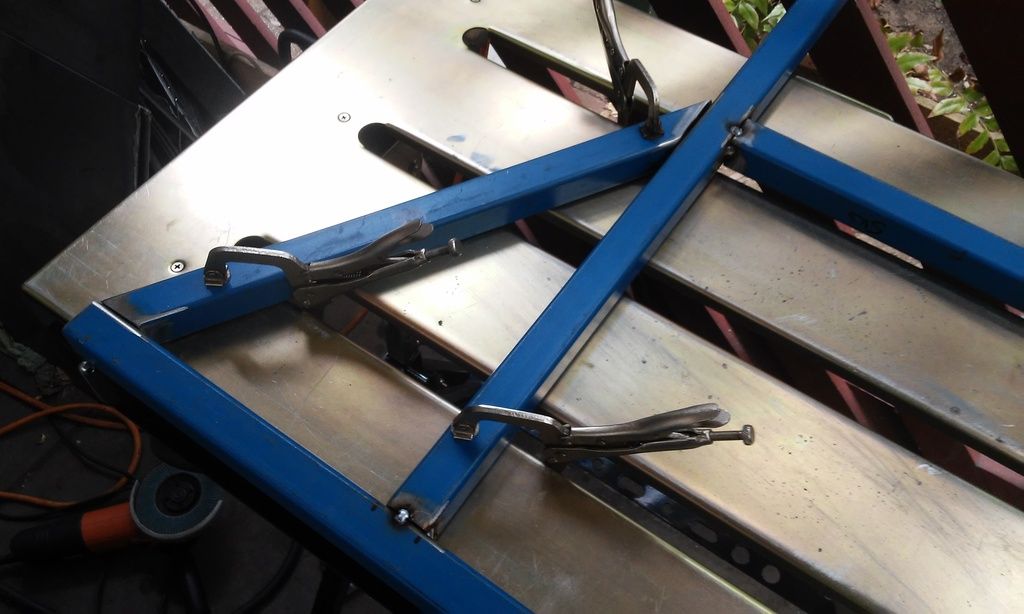