Hole repairs
Hole repairs
I have bitten the proverbial bullet and decided to finally do something about the metallic paint on the roof of the MY Touring wagon.
This unfortunately means the removal of the notorious luggage racks screwed to the roof of the car and the repair of all the holes.
There are obvious issues around some of the screw holes that will need some surface rust removal
I have something like 20 screw holes to fix.
While some body filler will be required, minimising this would be an advantage.
Has anyone use the likes of aluminium rivets to fill holes ?
I would imaging indenting where each hole is (concaving), putting the rivet in and affix, apply the filler, sand back and paint.
I do not have the option of welding the holes up so I am looking for a logical alternative.
Any other suggestions ?
Obvious is to remove any existing rust and rust prep each hole with my favourite "Rust in peace" rust treatment.
I would also be looking for aluminium rivets with stainless steel shafts and not mild steel.
This unfortunately means the removal of the notorious luggage racks screwed to the roof of the car and the repair of all the holes.
There are obvious issues around some of the screw holes that will need some surface rust removal
I have something like 20 screw holes to fix.
While some body filler will be required, minimising this would be an advantage.
Has anyone use the likes of aluminium rivets to fill holes ?
I would imaging indenting where each hole is (concaving), putting the rivet in and affix, apply the filler, sand back and paint.
I do not have the option of welding the holes up so I am looking for a logical alternative.
Any other suggestions ?
Obvious is to remove any existing rust and rust prep each hole with my favourite "Rust in peace" rust treatment.
I would also be looking for aluminium rivets with stainless steel shafts and not mild steel.
OK, more googling has revealed welding is best (obvious I know) or use like materials, ie, steel rivets on steel body work if the riveting method is chosen.
I am not exactly keen on rivets, just looking for options and am also wondering on fibreglass filler especially if I can get to the rear of the holes.
If I can prep the holes properly with the rust converter (if rust is present) or enlarge holes to get rid of minor rust, I may be able to stuff the fibreglass filler down the holes enough to support the filler from running down the hole.
The holes are only 3 to 4mm diameter so not real big.
I am loathing trying to pull the liner or even if I can get it down enough to get behind it but will try.
Again, welding is not an option. There is no way I will be pulling the liner all the way out in order to weld without setting something on fire or distorting the roof with all the heat.
I am not exactly keen on rivets, just looking for options and am also wondering on fibreglass filler especially if I can get to the rear of the holes.
If I can prep the holes properly with the rust converter (if rust is present) or enlarge holes to get rid of minor rust, I may be able to stuff the fibreglass filler down the holes enough to support the filler from running down the hole.
The holes are only 3 to 4mm diameter so not real big.
I am loathing trying to pull the liner or even if I can get it down enough to get behind it but will try.
Again, welding is not an option. There is no way I will be pulling the liner all the way out in order to weld without setting something on fire or distorting the roof with all the heat.
- d_generate
- General Member
- Posts: 1529
- Joined: Sat Feb 16, 2008 1:51 am
- Location: Back in Perth and SORing it atm.
What about those 2 pack metal fillers that can be drilled and filed, you punch the holes in your roof down then fill the indentation with the metal filler, hit it with a sander/grinder when it's dry then bog over it?
98 Libbo with V3 STI running gear. 13.0 @ 105mph with CAI & 3" Zorst:mrgreen:
http://www.youtube.com/watch?v=TKrsF-2JS3M
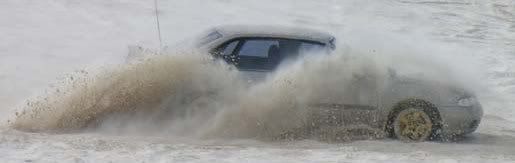
http://www.youtube.com/watch?v=TKrsF-2JS3M

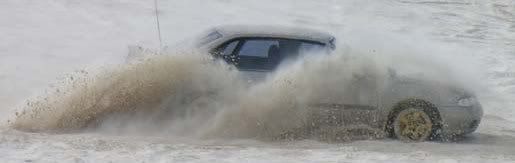
- Bantum
- Senior Member
- Posts: 2009
- Joined: Sun Jul 29, 2012 4:30 pm
- Location: Northern Territory + QLD
- Contact:
Yep +1 for welding, it's the only option long term - any other method will see you having to revisit when it eventually fails.
If done correctly it shouldn't be a problem for a good Tig welder, as they will be able to do it quick & easily without too much heat distortion going on.
Also it's not that hard to remove the lining, as its mostly held in place by clips & screws - just have to be careful of plastic trims that can be a little brittle ...
What are you plans with the old rack ?
Cheers, Bantum ...
If done correctly it shouldn't be a problem for a good Tig welder, as they will be able to do it quick & easily without too much heat distortion going on.
Also it's not that hard to remove the lining, as its mostly held in place by clips & screws - just have to be careful of plastic trims that can be a little brittle ...

What are you plans with the old rack ?
Cheers, Bantum ...
Removing the liner will be my first effort.
Not sure though if the liner went in before the rear windows so don't know if this will effect my efforts.
I have no interest in the old rack its never going back on as I want something like Rola racks off something/anything.
As long as I can get the height (high roof Touring wagon) in the rack uprights I can cut the cross beams to fit.
Anyone had any luck removing the chrome gutter trims and putting them back on later with an MY wagon ?
Not sure though if the liner went in before the rear windows so don't know if this will effect my efforts.
I have no interest in the old rack its never going back on as I want something like Rola racks off something/anything.
As long as I can get the height (high roof Touring wagon) in the rack uprights I can cut the cross beams to fit.
Anyone had any luck removing the chrome gutter trims and putting them back on later with an MY wagon ?
- Silverbullet
- Senior Member
- Posts: 2922
- Joined: Mon Aug 23, 2010 6:20 pm
- Location: Adelaide
Well I have taken them off, not put them back on yetCliff R wrote:Anyone had any luck removing the chrome gutter trims and putting them back on later with an MY wagon ?

Will it ever end!?
-EA81 TWIN CARB!!!!
-L series 5 speed
-Custom paint job
-2" lift
-Full custom re-wire
-L series front end
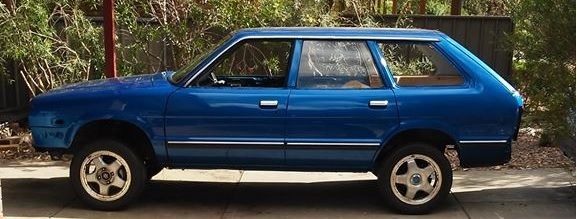
-EA81 TWIN CARB!!!!
-L series 5 speed
-Custom paint job
-2" lift
-Full custom re-wire
-L series front end
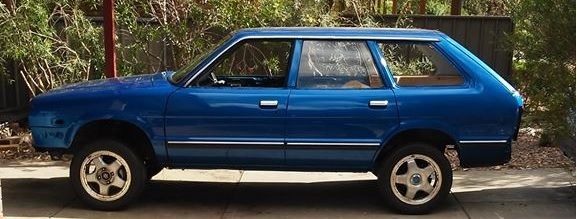
SIGH !!!!
What can I say.....
The decision on how to fix the screw on roof rack rails and rack holes is now taken out of my hands.
I pulled the rails and rack off, ground things down and found the following.
I need to save some cash and take the car to a panel beater and have the holes sorted with a TIG.
No idea on what this will cost.
The aim will be to get all the holes welded up and the roof prepped up with undercoat and ready for painting.
I will paint it from there.
Anyone with these damn screw on racks and rails should consider if they really need them and if not GET RID OF THEM !!!!

Rust right across the middle set of roof rack rail holes

Close up of one of the holes, 5c as a size guide.

Another hole with the 5c as a size guide again.
What can I say.....
The decision on how to fix the screw on roof rack rails and rack holes is now taken out of my hands.
I pulled the rails and rack off, ground things down and found the following.
I need to save some cash and take the car to a panel beater and have the holes sorted with a TIG.
No idea on what this will cost.
The aim will be to get all the holes welded up and the roof prepped up with undercoat and ready for painting.
I will paint it from there.
Anyone with these damn screw on racks and rails should consider if they really need them and if not GET RID OF THEM !!!!
Rust right across the middle set of roof rack rail holes
Close up of one of the holes, 5c as a size guide.
Another hole with the 5c as a size guide again.
- Silverbullet
- Senior Member
- Posts: 2922
- Joined: Mon Aug 23, 2010 6:20 pm
- Location: Adelaide
Wow!
This is what happens when you drill a hole in bodywork and don't paint the bare edges of the hole! Were these dealer fitted roof racks? Factory fitted? You'd think they would know better.
So they need welding now, if you just had them welded only and did the grinding and filling yourself, it should not cost too much. If you want them to do the bodywork, rub it back and prime it as well then the cost goes up. Still less than a days work for a pro I would say. Not sure how far away the head lining is but you might want to consider removing it, in case the heat melts a hole in it/sets it on fire.

So they need welding now, if you just had them welded only and did the grinding and filling yourself, it should not cost too much. If you want them to do the bodywork, rub it back and prime it as well then the cost goes up. Still less than a days work for a pro I would say. Not sure how far away the head lining is but you might want to consider removing it, in case the heat melts a hole in it/sets it on fire.
Will it ever end!?
-EA81 TWIN CARB!!!!
-L series 5 speed
-Custom paint job
-2" lift
-Full custom re-wire
-L series front end
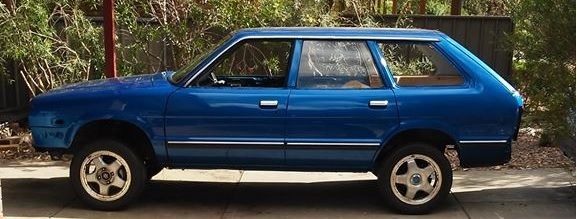
-EA81 TWIN CARB!!!!
-L series 5 speed
-Custom paint job
-2" lift
-Full custom re-wire
-L series front end
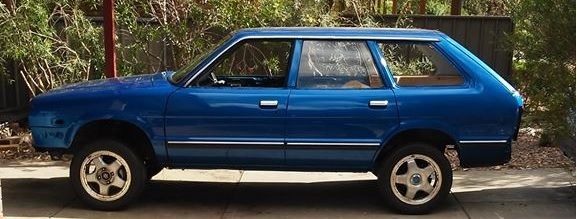
Silerbullet
I will get a price on, as you suggest, welding the holes and I go from there and a price to everything up to ready to paint including undercoat.
I don't know if the racks were put on in the factory or the dealer as we bought the car second hand in 1998.
I just know I have never found anything useful for them to carry..
I still have to work out how to deal with the liner so I don't know about this yet.
P1ayer
One thing I have learnt over this is there appears to be a channel running across the roof.
As a matter of fact I imaging there are a number of them where every line of screw holes run.
Devcon is great stuff but I am concerned on filling these channels up and if they are part of a drainage system blocking this up too.
I guess I am once bitten twice shy and if this isn't treated correctly now I could end up with the same thing again later.
I also recall with the roof rails taken off there is flex in then roof on bumps so I would be inclined to have a spot of weld put down each screw hole to simulate the screw being in place and attach the roof to each of the cross rails.
I will get a price on, as you suggest, welding the holes and I go from there and a price to everything up to ready to paint including undercoat.
I don't know if the racks were put on in the factory or the dealer as we bought the car second hand in 1998.
I just know I have never found anything useful for them to carry..
I still have to work out how to deal with the liner so I don't know about this yet.
P1ayer
One thing I have learnt over this is there appears to be a channel running across the roof.
As a matter of fact I imaging there are a number of them where every line of screw holes run.
Devcon is great stuff but I am concerned on filling these channels up and if they are part of a drainage system blocking this up too.
I guess I am once bitten twice shy and if this isn't treated correctly now I could end up with the same thing again later.
I also recall with the roof rails taken off there is flex in then roof on bumps so I would be inclined to have a spot of weld put down each screw hole to simulate the screw being in place and attach the roof to each of the cross rails.
- Bantum
- Senior Member
- Posts: 2009
- Joined: Sun Jul 29, 2012 4:30 pm
- Location: Northern Territory + QLD
- Contact:
Holy ...
Most likely dealer, although they are listed as factory options ...Cliff R wrote:... I don't know if the racks were put on in the factory or the dealer ...

It's not that hard - just remove all the trims, screws, etc + you may have to 'unstick' it from the front / side window seals and slide out the rear ...Cliff R wrote:... I still have to work out how to deal with the liner ...

They're only to keep the shape of roof + wont be that many, only 2 or 3 ( you'll see once the liners removed ) & are not drains ...Cliff R wrote:... One thing I have learnt over this is there appears to be a channel running across the roof ...

The rails are only 'glued' on the top side ( are fixed at ends ) so welding them will only create problems with not allowing the roof to flex ...Cliff R wrote:... inclined to have a spot of weld put down each screw hole to simulate the screw being in place and attach the roof to each of the cross rails.

Cheers, Bantum ...
The last time I had a car at a panel beaters was in about 1985 after being T boned by someone who thought a red light meant green and go.
Anyone got a feel for the current pricing for car repairs. ?
I didn't want the car to go for a quote until I had some cash behind me.
I think my 14's have been sold and a ride on mower engine just got bought so when the cash comes in I look to have about $500.
Is this libel to get me far ?
The 2 options are for the holes to be welded up and that's it or the holes to be welded up filled and prepped/undercoated ready for painting.
I would prefer the second option as it is less work for me but I will go for whatever I can with the cash on hand.
Anyone got a feel for the current pricing for car repairs. ?
I didn't want the car to go for a quote until I had some cash behind me.
I think my 14's have been sold and a ride on mower engine just got bought so when the cash comes in I look to have about $500.
Is this libel to get me far ?
The 2 options are for the holes to be welded up and that's it or the holes to be welded up filled and prepped/undercoated ready for painting.
I would prefer the second option as it is less work for me but I will go for whatever I can with the cash on hand.
Update on the holes in the roof.
- Nothing
Yep, I have done absolutely nothing.
I started the car yesterday and as it has been sitting in the garage since August it wasn't exactly happy about starting and the battery was flat but got there in the end.
Anyway, I am still in two minds on who will carry out these repairs so I have a question someone may be able to answer.
I am already reasonably skilled in MIG welding and since I understand MIG is easier to use and creates less heat distortion than TIG, I am thinking of carrying out the work myself.
This may or may not be cheaper than a panel beater (see question below) but I will have full control on what is done, how it is done and when it is done.
The only issue with this is, I already have 2 MIG welders but.....
One is gasless and only good for 0.9mm wire which is too big for car steel and the other machine is gas/gasless but fairly worn out from years of use.
I am interested in buying a new MIG anyway to replace the worn out unit but I wouldn't mind some advice.
Can anyone recommend a decent, small gassed MIG welder (can then do 0.6mm, ie, small wire) where the gas can be supplied by disposable cans and the machine is 10A powered (I don't have access to a 15A supply)
I am after a machine with reasonable support and spares for things like tips an shrouds etc.
Also, for those electrical minded people do welders such as MIG's set house power box RCD's off (trip out) and if so is it then necessary to install an unprotected power source.
- Nothing
Yep, I have done absolutely nothing.
I started the car yesterday and as it has been sitting in the garage since August it wasn't exactly happy about starting and the battery was flat but got there in the end.
Anyway, I am still in two minds on who will carry out these repairs so I have a question someone may be able to answer.
I am already reasonably skilled in MIG welding and since I understand MIG is easier to use and creates less heat distortion than TIG, I am thinking of carrying out the work myself.
This may or may not be cheaper than a panel beater (see question below) but I will have full control on what is done, how it is done and when it is done.
The only issue with this is, I already have 2 MIG welders but.....
One is gasless and only good for 0.9mm wire which is too big for car steel and the other machine is gas/gasless but fairly worn out from years of use.
I am interested in buying a new MIG anyway to replace the worn out unit but I wouldn't mind some advice.
Can anyone recommend a decent, small gassed MIG welder (can then do 0.6mm, ie, small wire) where the gas can be supplied by disposable cans and the machine is 10A powered (I don't have access to a 15A supply)
I am after a machine with reasonable support and spares for things like tips an shrouds etc.
Also, for those electrical minded people do welders such as MIG's set house power box RCD's off (trip out) and if so is it then necessary to install an unprotected power source.
- Silverbullet
- Senior Member
- Posts: 2922
- Joined: Mon Aug 23, 2010 6:20 pm
- Location: Adelaide
I used .8mm wire for all my rust repairs without issue, so you shouldn't need to go right down to .6 mm. It's all in the settings and you have to pulse the trigger and not run one continuous weld. There's a bit of a problem in the sort of machine you want; all of the machines I've seen that fit your description (small, 10A supply) do not have enough fine adjustment on the settings for volts and amps to do thin stuff, just one knob that is supposed to control everything. I'm sure you already know but forget gassless wire for panel steel, it's not meant for that anyway.
I haven't used many small machines, only the one I bought so it's the only one I can recommend which was a Cigweld transmig 175i, has an inbuilt inverter and can do all 3 welding processes. Maybe a bit pricey for what you were expecting. I think Cig do similar machines that are only MIG machines, might pay to have a look at their catalogue. I would absolutely stay away from the machines at Funnings they may be cheap but they are garbage. I can guarantee if you tried to fix your roof with one of them you'd be frustrated. But if you want to have a decent welder for future projects, definitely have alook at the Cigweld machines as they have excellent support for spares, mine even came with 4 different sizes of feed rollers and tips for whatever wire I want to use.
As for power, I've found not many of the decent machines take 10A, only 15A (just has the bigger earth terminal) Therefore I made a very short adapter lead (as was recommended by the place I bought the machine) 15A female at one end an 10A male at the other. I've had my machine cranked right up to full power and could weld all day without tripping the breakers, but that was with the inverter inside not an old transformer type. At the welding shop they had a 250A inverter hooked up to the 240V the same way, through the 10A plug, and everyone I've spoken to about it says there is no problem as long as the wiring in your house can take it. Our circuit breakers are rated at 20A or something so no problems there.
I haven't used many small machines, only the one I bought so it's the only one I can recommend which was a Cigweld transmig 175i, has an inbuilt inverter and can do all 3 welding processes. Maybe a bit pricey for what you were expecting. I think Cig do similar machines that are only MIG machines, might pay to have a look at their catalogue. I would absolutely stay away from the machines at Funnings they may be cheap but they are garbage. I can guarantee if you tried to fix your roof with one of them you'd be frustrated. But if you want to have a decent welder for future projects, definitely have alook at the Cigweld machines as they have excellent support for spares, mine even came with 4 different sizes of feed rollers and tips for whatever wire I want to use.
As for power, I've found not many of the decent machines take 10A, only 15A (just has the bigger earth terminal) Therefore I made a very short adapter lead (as was recommended by the place I bought the machine) 15A female at one end an 10A male at the other. I've had my machine cranked right up to full power and could weld all day without tripping the breakers, but that was with the inverter inside not an old transformer type. At the welding shop they had a 250A inverter hooked up to the 240V the same way, through the 10A plug, and everyone I've spoken to about it says there is no problem as long as the wiring in your house can take it. Our circuit breakers are rated at 20A or something so no problems there.
Will it ever end!?
-EA81 TWIN CARB!!!!
-L series 5 speed
-Custom paint job
-2" lift
-Full custom re-wire
-L series front end
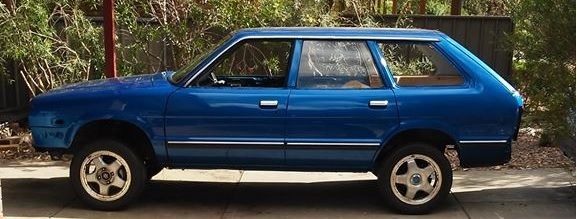
-EA81 TWIN CARB!!!!
-L series 5 speed
-Custom paint job
-2" lift
-Full custom re-wire
-L series front end
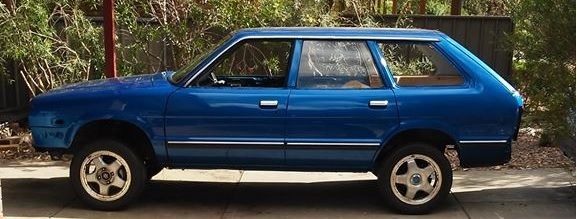